Why We Treat WIP Like That Mysterious Tuna Casserole in the Fridge
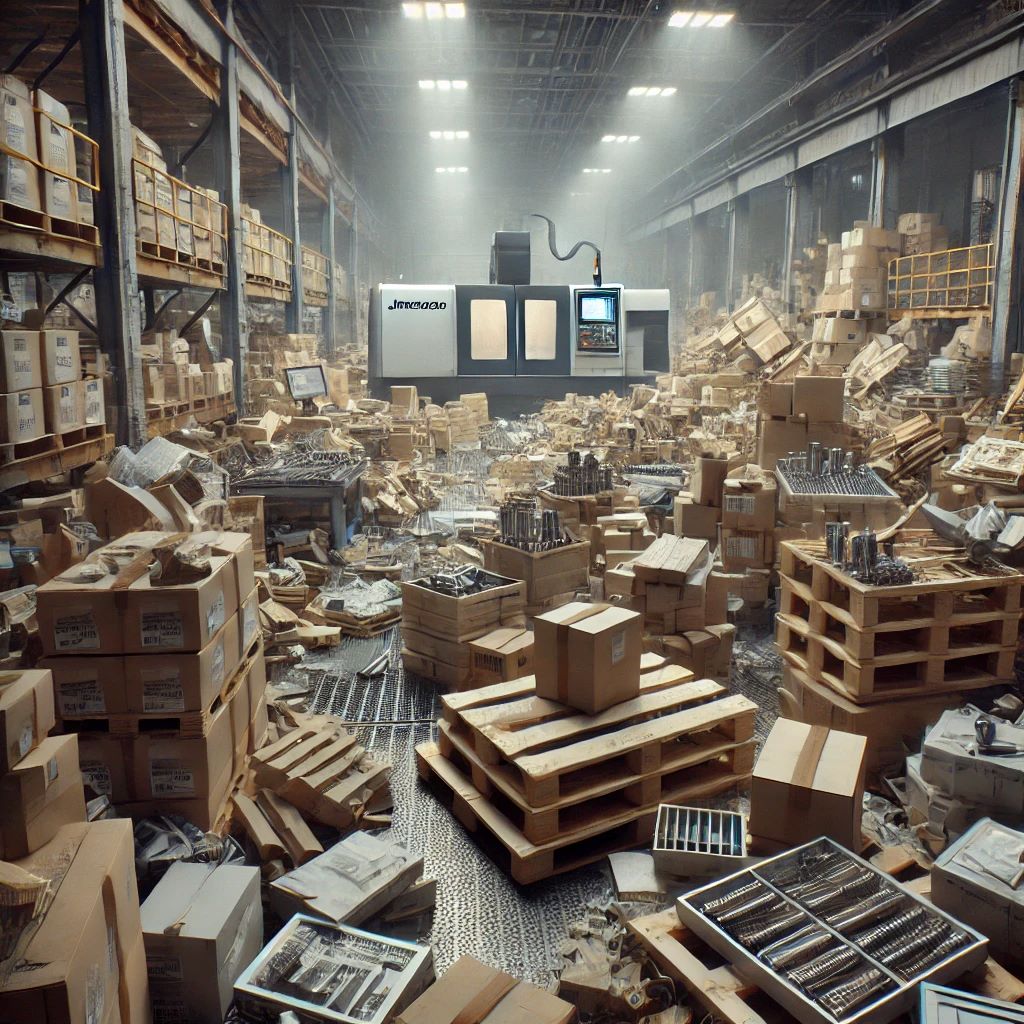
At American Precision Engineering, we’re no strangers to multitasking. With tools, hardware, and materials flying in from every direction, it’s tempting to dive into a project even if all the pieces aren’t in place.
Maybe the PEM hardware hasn’t arrived yet, but you’re thinking, “No problem! Let’s cut the parts and get a head start!” Or you’re running all parts through OP1 on the CNC while waiting for the OP2 tool, feeling pretty proactive!
Sounds efficient, right? But here’s the deal: we avoid WIP like it’s a three-week-old tuna casserole sitting in the back of the fridge.
Wait… What’s WIP?
WIP stands for Work-In-Process. It’s the fancy term for unfinished inventory—essentially, cash tied up in metal parts that are collecting dust on pallets. And trust us, the last thing you want is a shop floor full of WIP.
Why WIP is the Villain of Manufacturing
1. It’s Wasteful.
WIP hogs space, clutters racks, and turns your team into full-time inventory wranglers. More WIP means extra handling, extra tracking, and—let’s be honest—extra frustration. Instead of creating precision-engineered parts, your team ends up playing Tetris with half-finished projects.
2. It Encourages Overproduction.
Imagine you’re cranking out extra parts in step 1, just in case something goes wrong in step 4. That’s a noble thought, but here’s the problem: you’re almost always making way more than you need. That’s not just inefficient—it’s waste, plain and simple.
3. Welcome to Scrap City.
Now for the worst-case scenario: you blast through steps 1, 2, and 3, only to realize at step 4 that everything is completely wrong.
Without the final components to verify along the way, you’re basically rolling the dice on the entire project. And with the kind of complex, one-off work we do at APE, the odds of everything being perfect on the first try? Let’s just say they’re not in our favor. The cost of starting over? A heart-wrenching trip to Scrap City.
So, What’s the Bottom Line?
If you don’t have everything you need to finish the job and verify that it’s right, DON’T START. Seriously. Put down the tools, step away from the CNC machine, and wait for the missing pieces.
At APE, our mission isn’t to look busy. It’s to deliver precise, high-quality results without risking a mountain of expensive scrap metal. We’d rather take the time to do it right the first time than rush into a mess of half-finished work.
So the next time you’re tempted to jump the gun, remember: WIP is like a bad casserole—it might seem harmless at first, but you’ll regret it later.
At American Precision Engineering, we’re no strangers to multitasking. With tools, hardware, and materials flying in from every direction, it’s tempting to dive into a project even if all the pieces aren’t in place.
Maybe the PEM hardware hasn’t arrived yet, but you’re thinking, “No problem! Let’s cut the parts and get a head start!” Or you’re running all parts through OP1 on the CNC while waiting for the OP2 tool, feeling pretty proactive!
Sounds efficient, right? But here’s the deal: we avoid WIP like it’s a three-week-old tuna casserole sitting in the back of the fridge.
Wait… What’s WIP?
WIP stands for Work-In-Process. It’s the fancy term for unfinished inventory—essentially, cash tied up in metal parts that are collecting dust on pallets. And trust us, the last thing you want is a shop floor full of WIP.
Why WIP is the Villain of Manufacturing
1. It’s Wasteful.
WIP hogs space, clutters racks, and turns your team into full-time inventory wranglers. More WIP means extra handling, extra tracking, and—let’s be honest—extra frustration. Instead of creating precision-engineered parts, your team ends up playing Tetris with half-finished projects.
2. It Encourages Overproduction.
Imagine you’re cranking out extra parts in step 1, just in case something goes wrong in step 4. That’s a noble thought, but here’s the problem: you’re almost always making way more than you need. That’s not just inefficient—it’s waste, plain and simple.
3. Welcome to Scrap City.
Now for the worst-case scenario: you blast through steps 1, 2, and 3, only to realize at step 4 that everything is completely wrong.
Without the final components to verify along the way, you’re basically rolling the dice on the entire project. And with the kind of complex, one-off work we do at APE, the odds of everything being perfect on the first try? Let’s just say they’re not in our favor. The cost of starting over? A heart-wrenching trip to Scrap City.
So, What’s the Bottom Line?
If you don’t have everything you need to finish the job and verify that it’s right, DON’T START. Seriously. Put down the tools, step away from the CNC machine, and wait for the missing pieces.
At APE, our mission isn’t to look busy. It’s to deliver precise, high-quality results without risking a mountain of expensive scrap metal. We’d rather take the time to do it right the first time than rush into a mess of half-finished work.
So the next time you’re tempted to jump the gun, remember: WIP is like a bad casserole—it might seem harmless at first, but you’ll regret it later.
GET YOUR APE FIX
Subscribe to our newsletter for the latest updates, events, and insider insights straight from the APE team.