Bag Filler
Rapid Problem-Solving for the World's Largest Electric Car Manufacturer
When the world's biggest electric car manufacturer encounters a problem, they don’t have the luxury of time. They need solutions immediately and can’t afford to wait for a slow design and build partner.
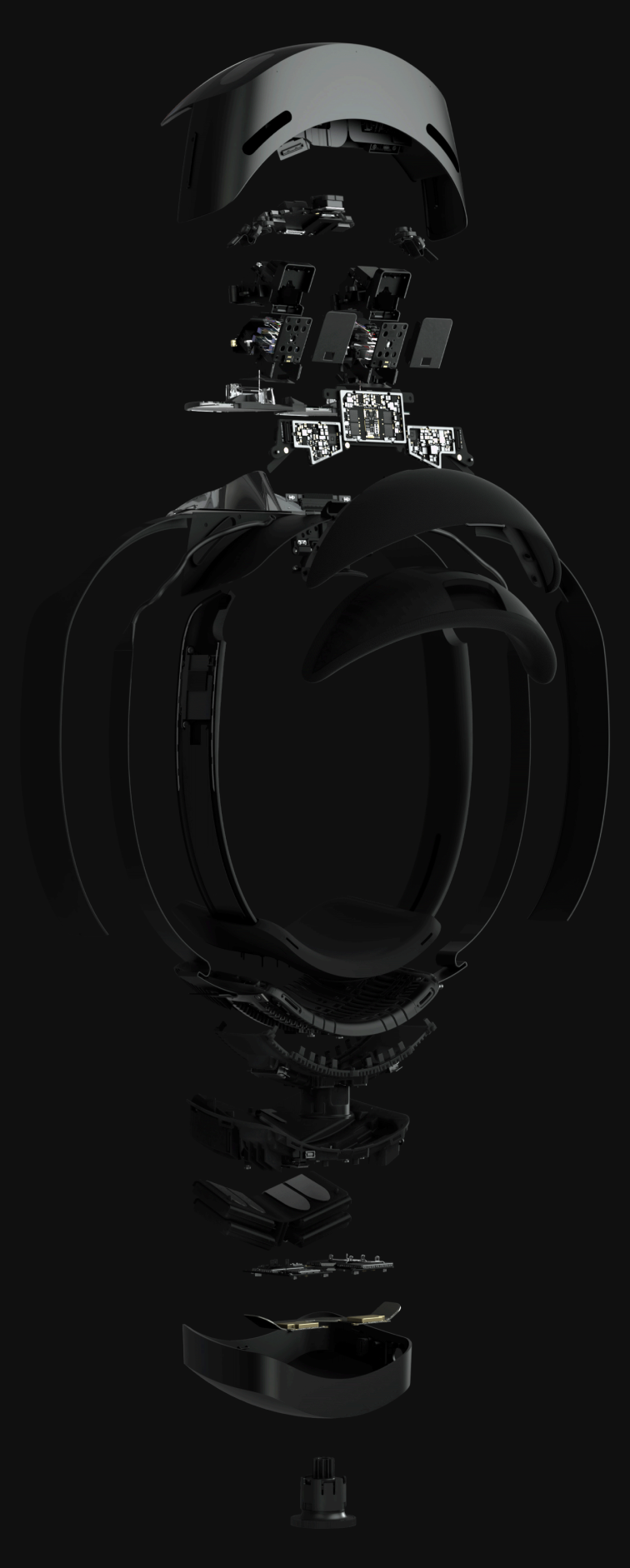
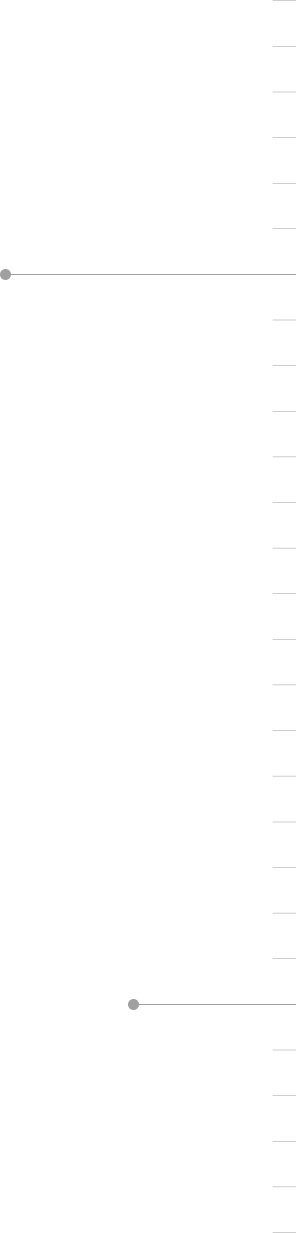
The Finished Product
Bag Filler
Rapid Problem-Solving for the World's Largest Electric Car Manufacturer
When the world's biggest electric car manufacturer encounters a problem, they don’t have the luxury of time. They need solutions immediately and can’t afford to wait for a slow design and build partner.
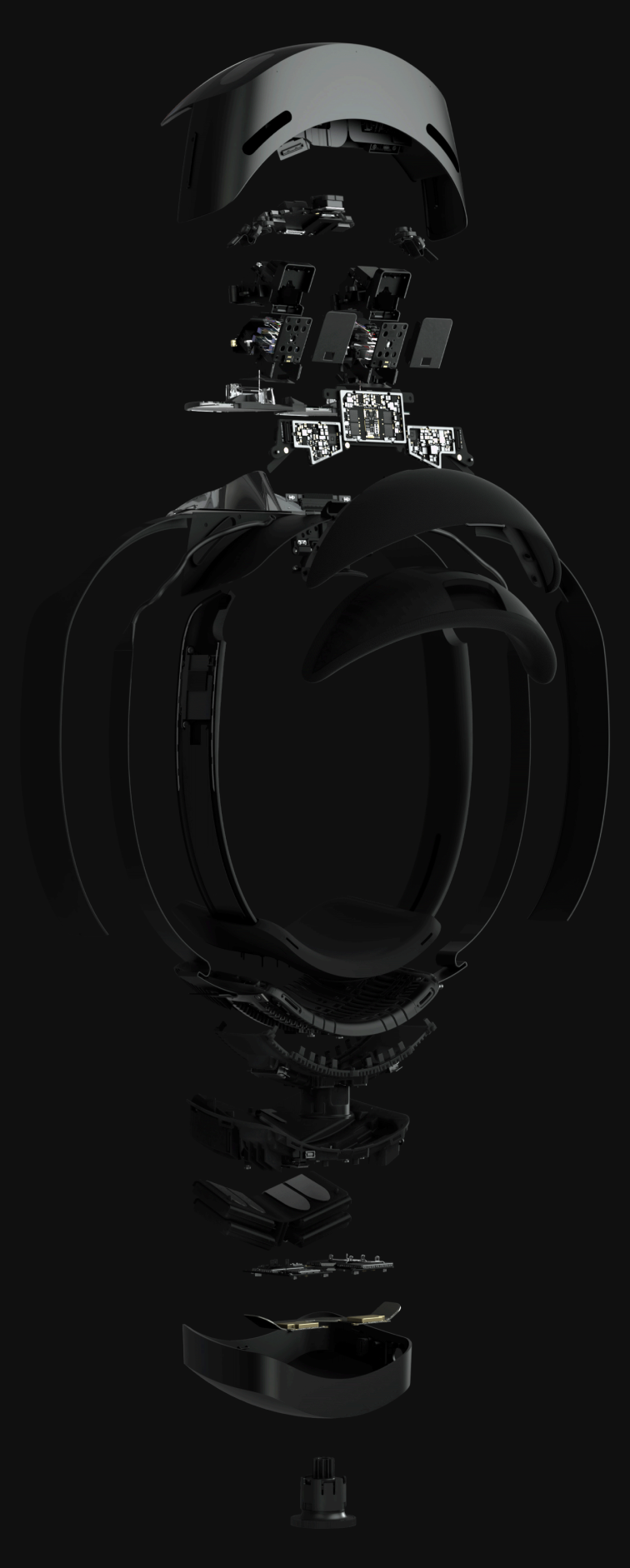
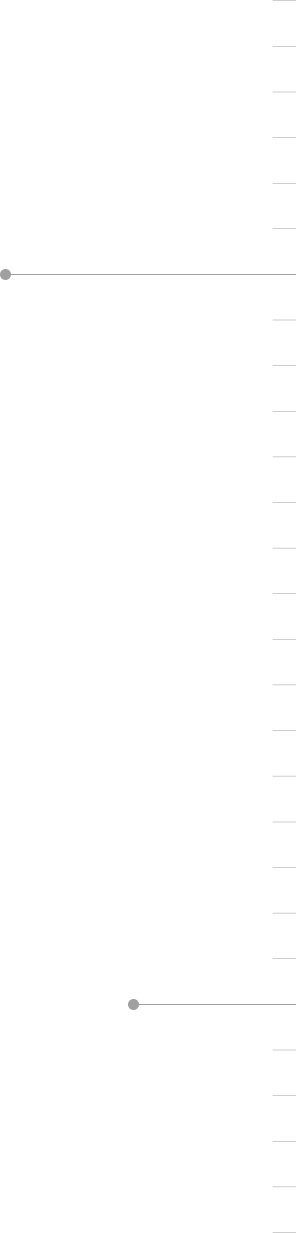
HOW WE MADE IT HAPPEN
In the fast-paced world of new product development, resources and time are often limited. To overcome these challenges, companies can turn to APE for expert assistance to accelerate their development processes. This case study highlights how APE supported a military vehicle manufacturer in meeting critical delivery deadlines by developing an efficient weld fixturing system and manufacturing process.
As the military vehicle manufacturer approached the final stages of designing their latest vehicle, they faced a significant hurdle. They lacked both the in-house expertise and the bandwidth to develop the necessary fixturing system and manufacturing process to meet their delivery requirements. Recognizing the urgency, they reached out to APE for a solution.
APE’s expertise in developing advanced weld fixtures exemplifies how strategic partnerships can enhance a company’s capabilities and accelerate product development. This collaboration underscores APE’s commitment to providing solutions that meet the most demanding industry standards and delivery requirements.
Contact us today to learn how APE can help accelerate your product development process.
The Finished Product
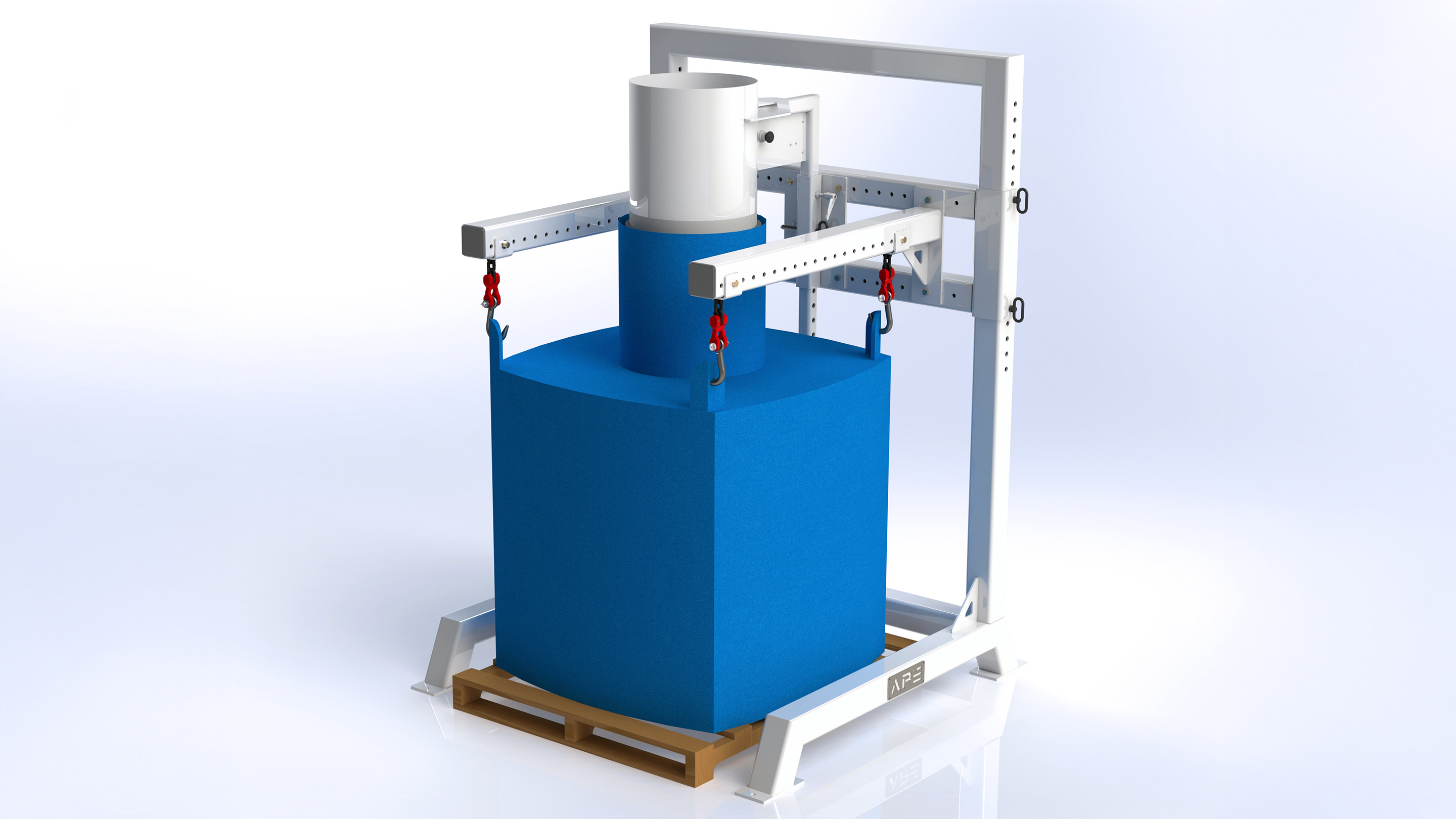
Bag Filler
Rapid Problem-Solving for the World's Largest Electric Car Manufacturer
When the world's biggest electric car manufacturer encounters a problem, they don’t have the luxury of time. They need solutions immediately and can’t afford to wait for a slow design and build partner.
The Finished Product
HOW WE MADE
IT HAPPEN
When the world's biggest electric car manufacturer encounters a problem, they don’t have the luxury of time. They need solutions immediately and can’t afford to wait for a slow design and build partner. That's why they turned to APE for a swift and effective resolution.
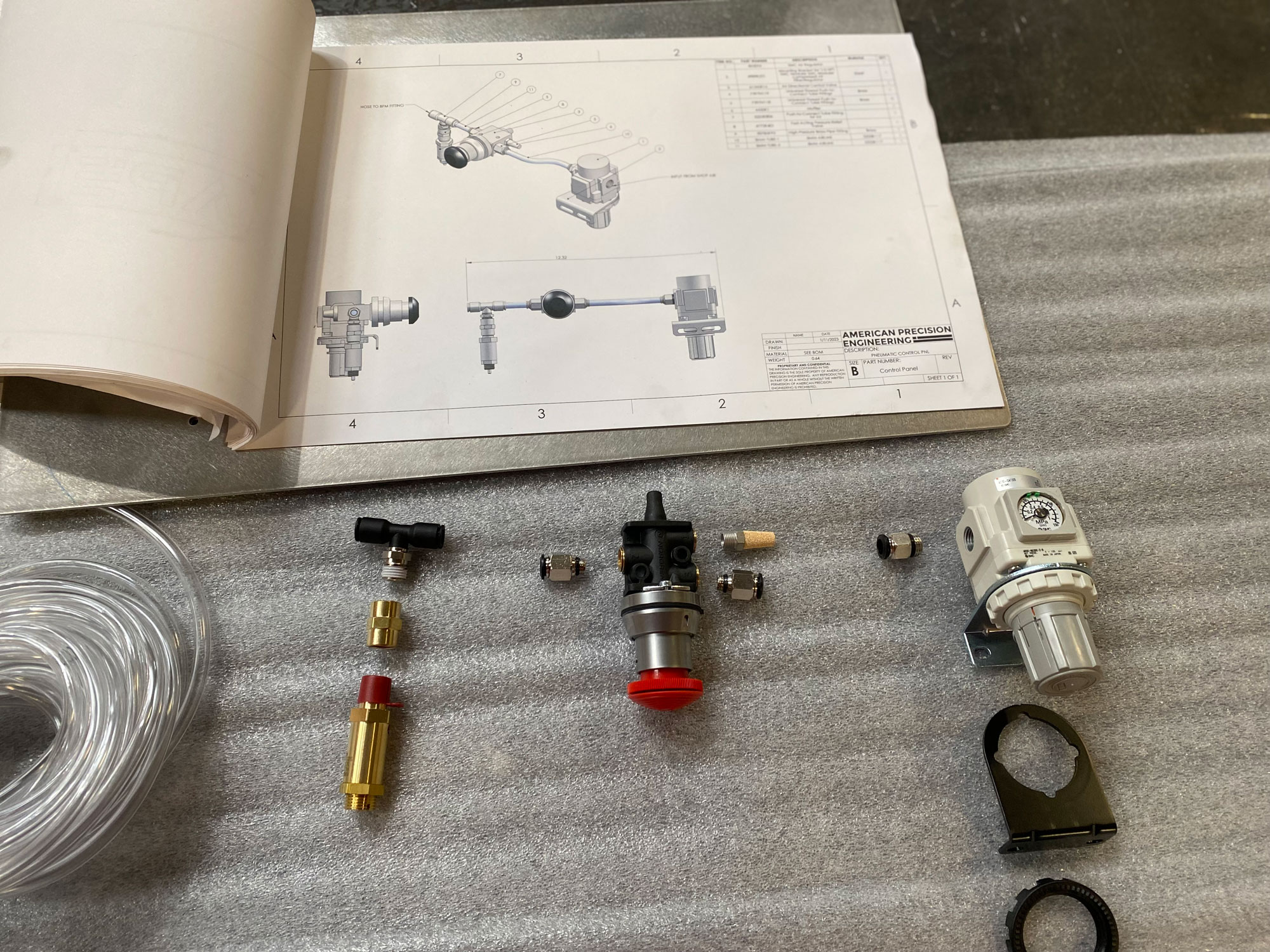
In their manufacturing process, a significant amount of fine dust was being captured by their dust collection system. However, they lacked a method to transfer this dust into a container for easy transportation. Additionally, because the dust was highly prone to becoming airborne, any connection to the bag had to be airtight to prevent contamination.
APE engineered a solution using our Design-Thru-Fab methodology, which ensures smooth fabrication through the use of simple details such as tab & slot features, poka-yoke elements, and clear shop drawings and assembly diagrams. The system was built with a 4-inch steel tube frame connected by laser-cut plates.
We developed a robust structure to hold a spigot top bulk bag in place with four hooks. The spigot top of the bag was sealed using a pneumatic bag sealer gasket. This gasket would expand to seal the inside of the spigot, allowing the dust to fill the bag while preventing any dust from escaping into the air. Once the bag was full, it could be detached from the frame within seconds and moved out of the room using a pallet jack or forklift.
Key Features:
- Laser Cut Tube Frame: A sturdy frame to hold the spigot top bulk bag securely.
- Pneumatic Bag Sealer Gasket: Ensures an airtight seal inside the spigot, allowing dust to fill the bag without escaping.
- Easy Detachment: The bag can be unhooked from the frame swiftly for easy removal and transportation.
- Simple Installation: The system features a standard duct flange and a single pneumatic hose connection, enabling it to be operational within minutes of delivery.
- User-Friendly Operation: A single button controls the bag sealer – press once to seal the bag and twist to release the pressure for bag removal.
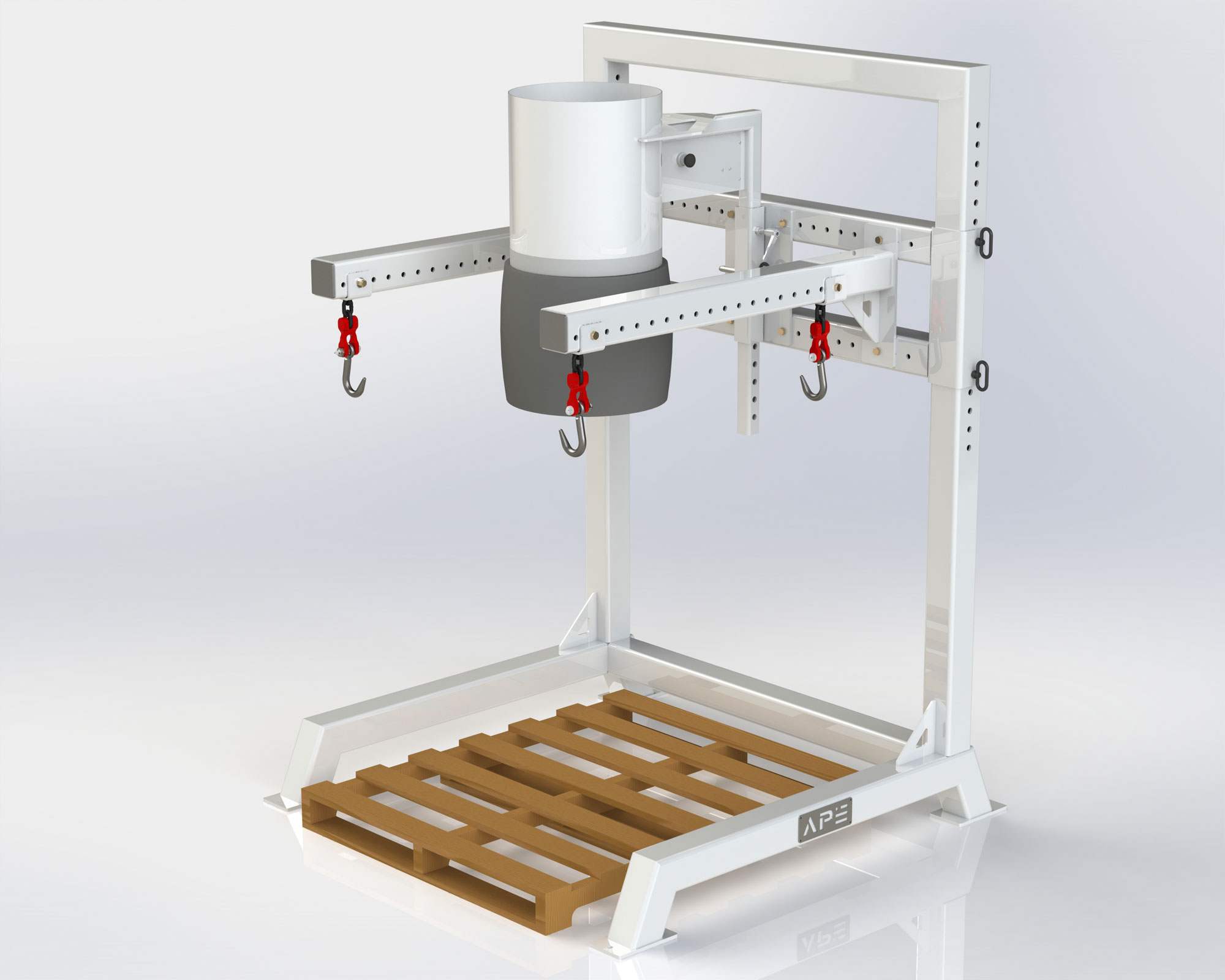
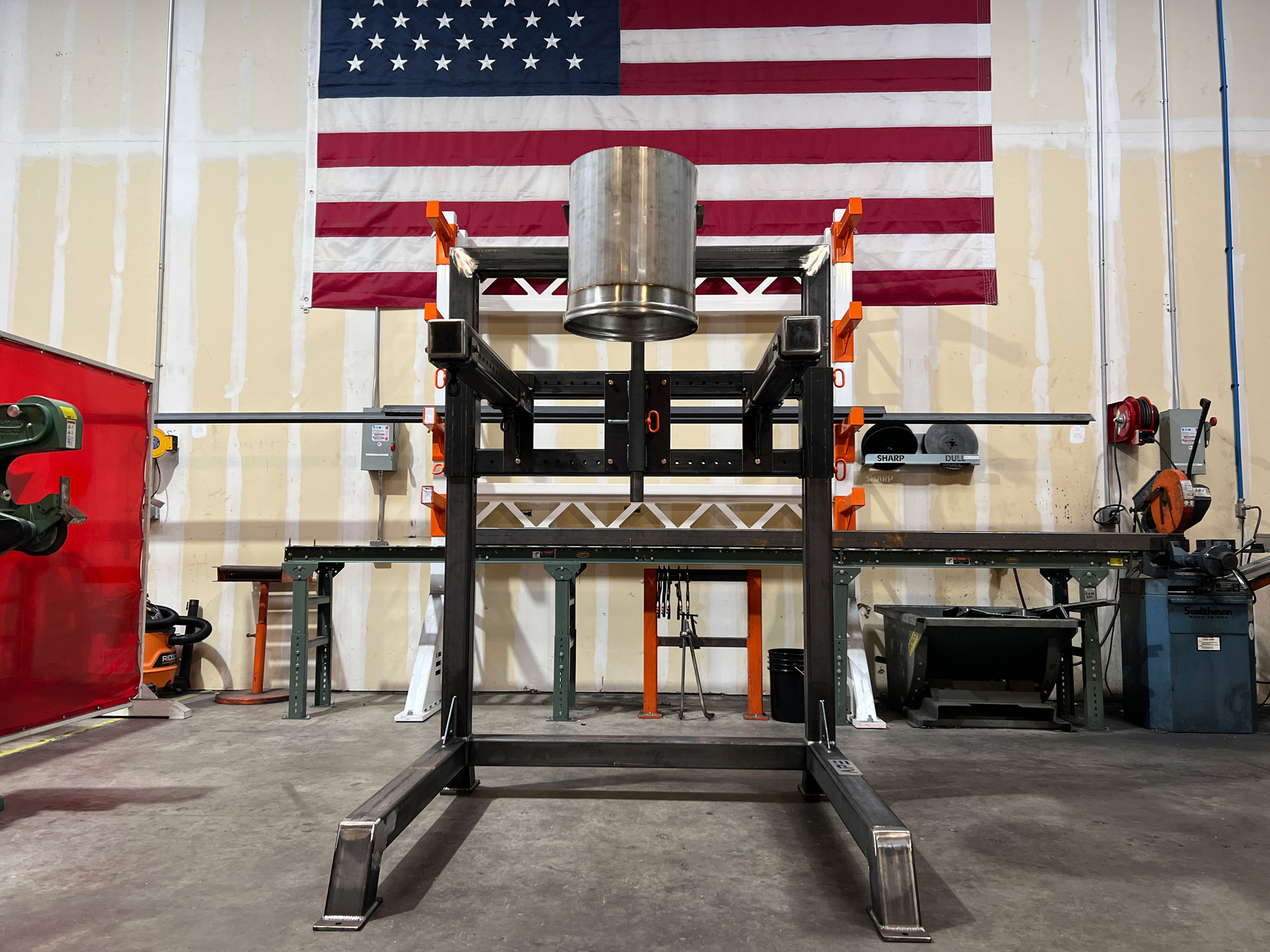
The electric car manufacturer received an easy-to-install, easy-to-use, and robust solution that not only saved them time but also improved safety at their facility. The swift installation and straightforward operation of the system ensured that their production process continued smoothly without significant downtime.
APE's ability to rapidly design and fabricate this solution highlights our commitment to meeting the urgent needs of our clients, providing innovative and practical solutions that enhance efficiency and safety.
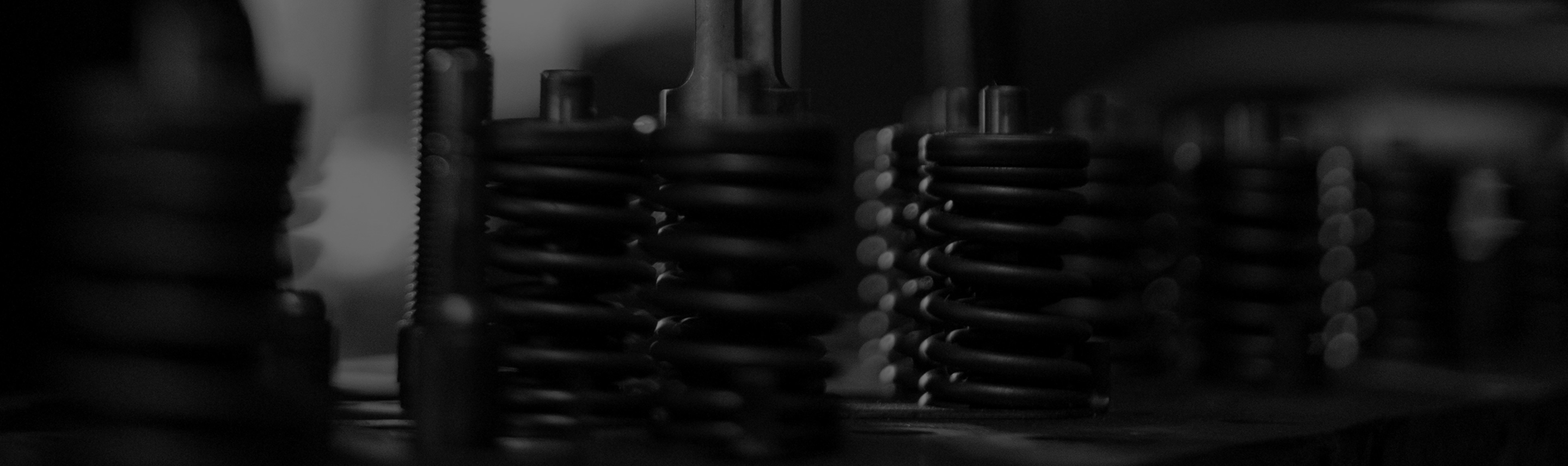
Related Case
Studies
Explore our recent case studies showcasing innovative solutions for advanced manufacturing.
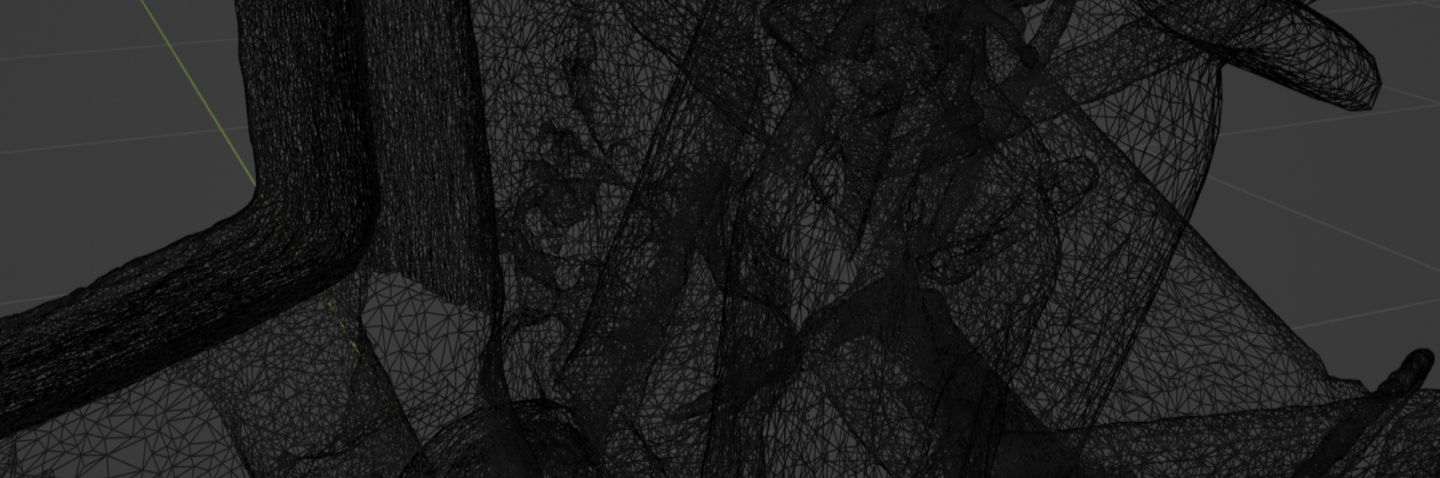
What Else Do We Do? Design And Engneering
Explore our comprehensive design and engineering services that lay the foundation for innovative and effective soluttions. From Concept to planning, every project is meticulously crafted to meet your needds.
Quality & Certifications
At APE, quality is woven into every part of our project life cycle. From design verification to the raw materials we use, to final assembly, our AS9100 certified quality management system... Read more