Weld Fixture Development
For Military Vehicle Manufacturer
In the fast-paced world of new product development, resources and time are often limited. To overcome these challenges, companies can turn to APE for expert assistance to accelerate their development processes.
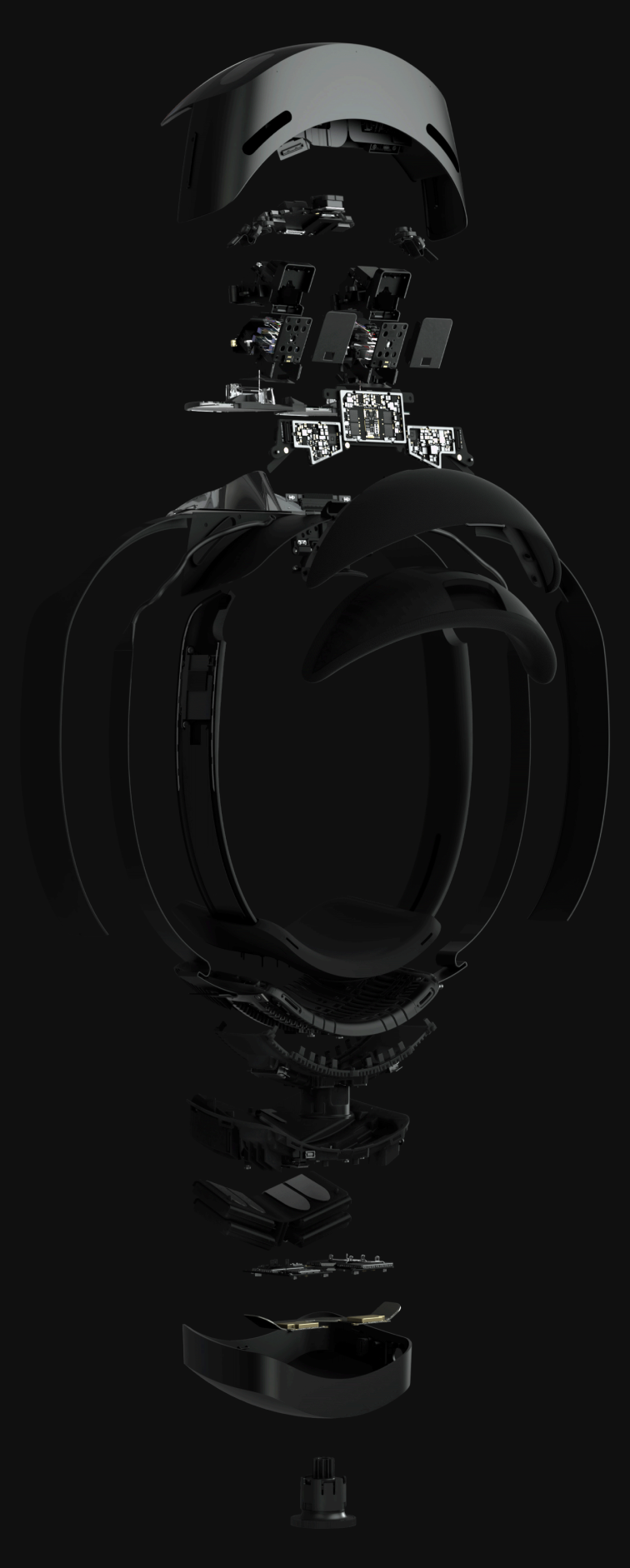
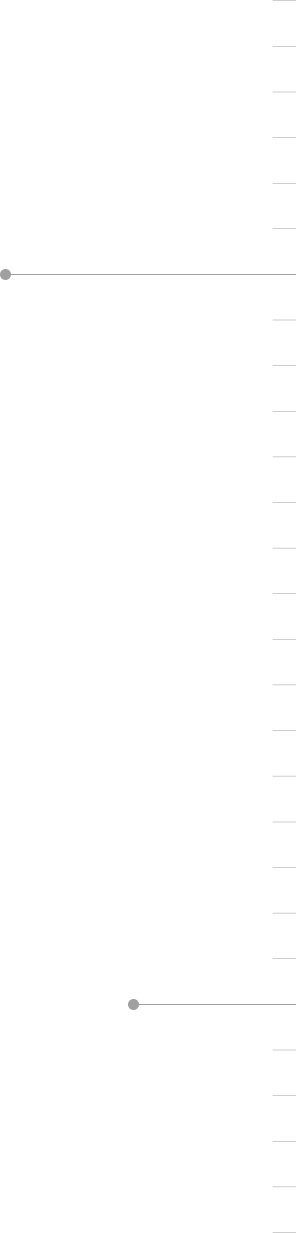
The Finished Product
Weld Fixture Development
For Military Vehicle Manufacturer
In the fast-paced world of new product development, resources and time are often limited. To overcome these challenges, companies can turn to APE for expert assistance to accelerate their development processes.
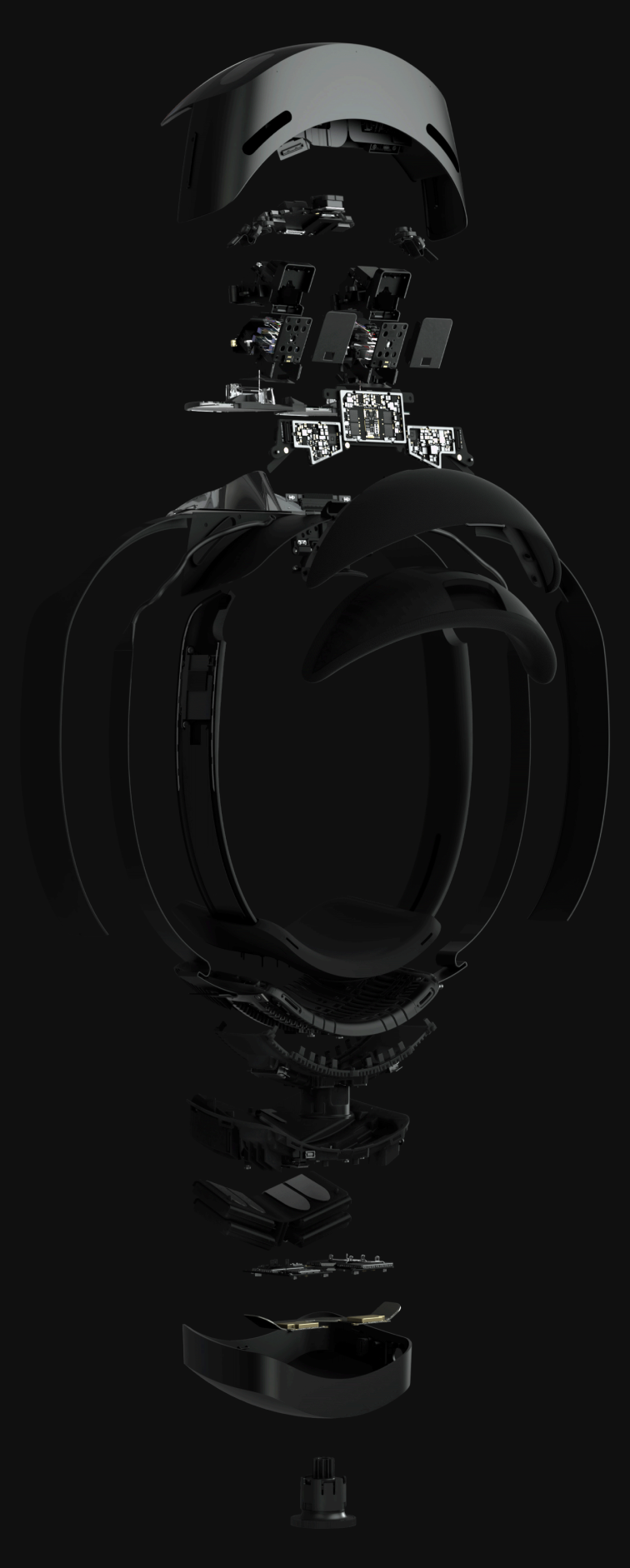
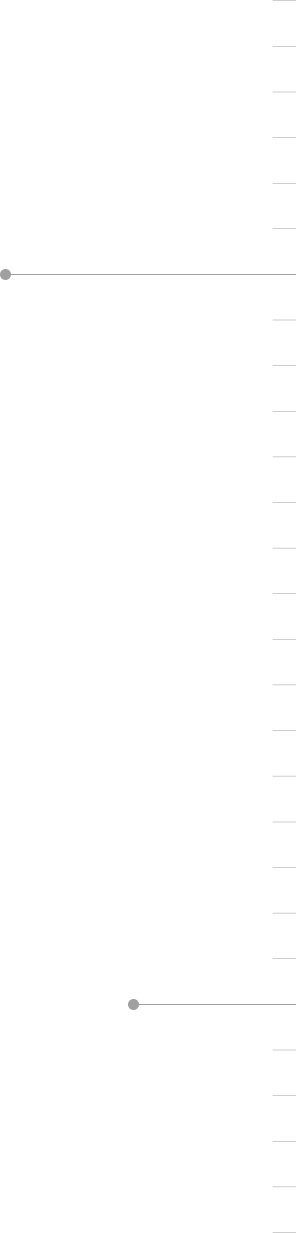
HOW WE MADE IT HAPPEN
In the fast-paced world of new product development, resources and time are often limited. To overcome these challenges, companies can turn to APE for expert assistance to accelerate their development processes. This case study highlights how APE supported a military vehicle manufacturer in meeting critical delivery deadlines by developing an efficient weld fixturing system and manufacturing process.
As the military vehicle manufacturer approached the final stages of designing their latest vehicle, they faced a significant hurdle. They lacked both the in-house expertise and the bandwidth to develop the necessary fixturing system and manufacturing process to meet their delivery requirements. Recognizing the urgency, they reached out to APE for a solution.
APE’s expertise in developing advanced weld fixtures exemplifies how strategic partnerships can enhance a company’s capabilities and accelerate product development. This collaboration underscores APE’s commitment to providing solutions that meet the most demanding industry standards and delivery requirements.
Contact us today to learn how APE can help accelerate your product development process.
The Finished Product
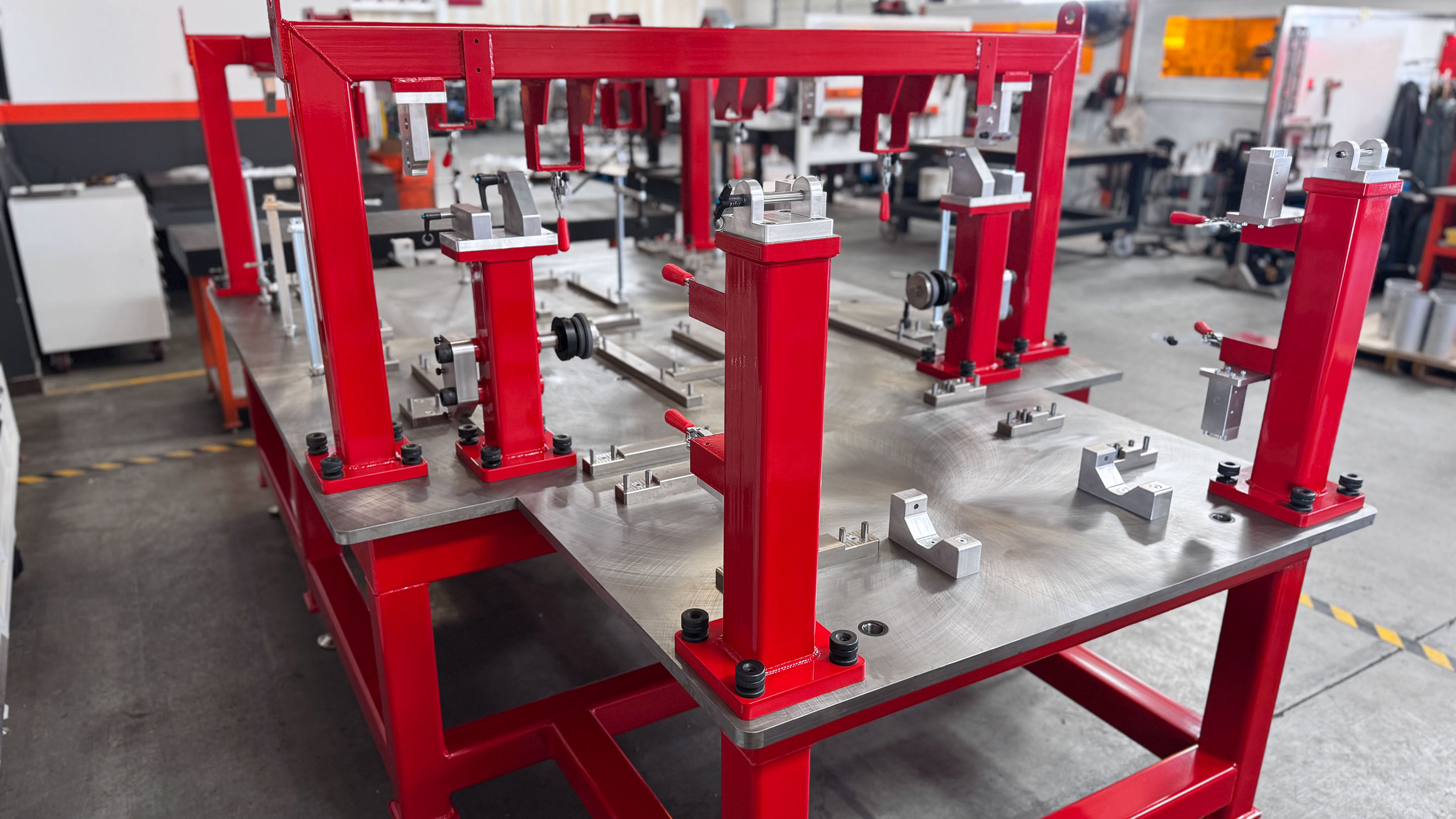
Weld Fixture Development
For Military Vehicle Manufacturer
In the fast-paced world of new product development, resources and time are often limited. To overcome these challenges, companies can turn to APE for expert assistance to accelerate their development processes.
The Finished Product
HOW WE MADE
IT HAPPEN
In the fast-paced world of new product development, resources and time are often limited. To overcome these challenges, companies can turn to APE for expert assistance to accelerate their development processes. This case study highlights how APE supported a military vehicle manufacturer in meeting critical delivery deadlines by developing an efficient weld fixturing system and manufacturing process.
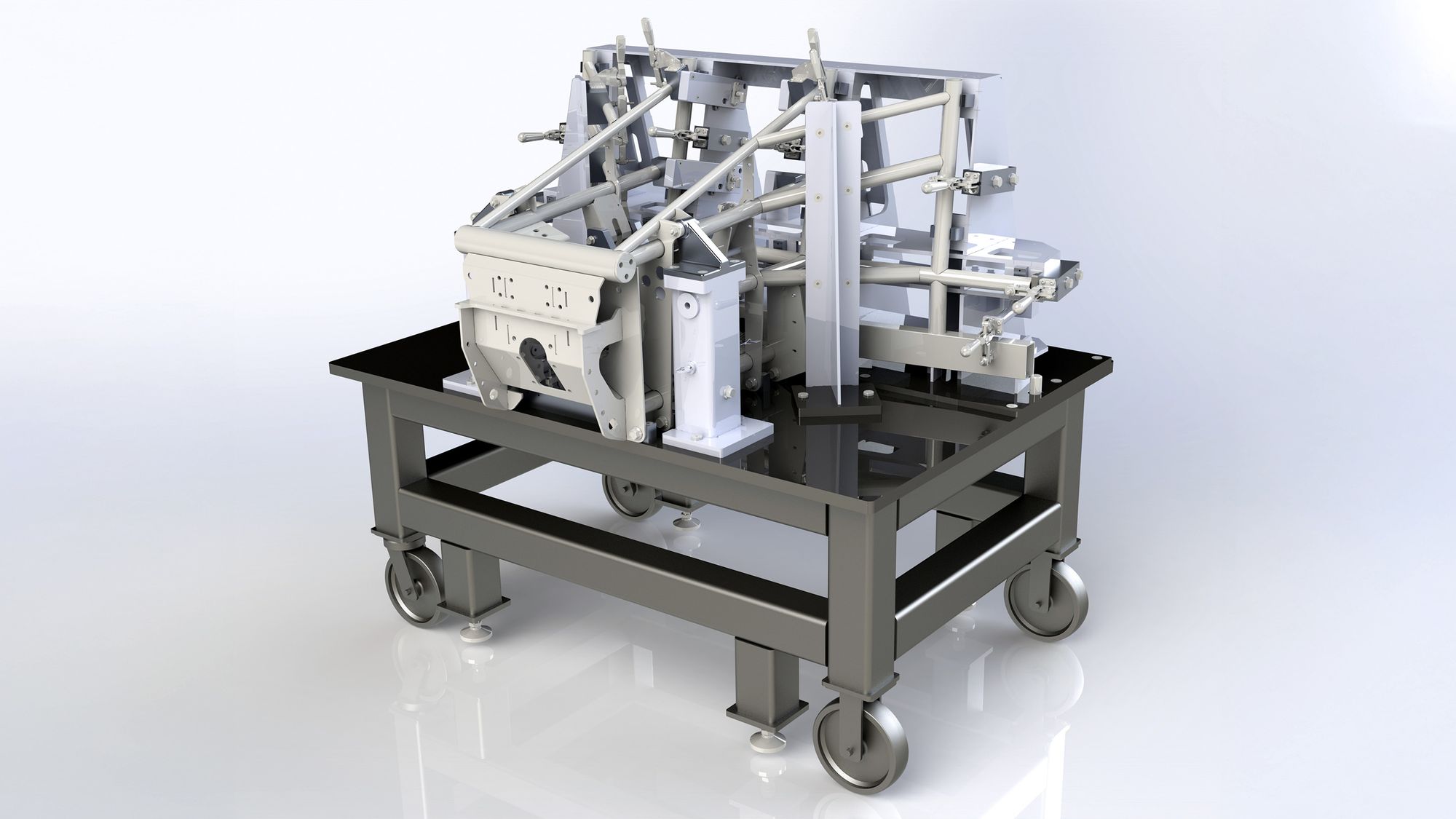
As the military vehicle manufacturer approached the final stages of designing their latest vehicle, they faced a significant hurdle. They lacked both the in-house expertise and the bandwidth to develop the necessary fixturing system and manufacturing process to meet their delivery requirements. Recognizing the urgency, they reached out to APE for a solution.
APE began by analyzing the client's design model, exploring various options for constructing the vehicle. After thorough evaluation, they established a build sequence and sub-assembly regime that satisfied all project stakeholders.
The vehicle was divided into manageable subassemblies, and each step in holding and fixturing these components for welding was meticulously planned. The primary consideration in designing a weld fixture is ensuring the precise positioning of parts throughout the welding process to prevent any movement. This is especially challenging in complex chassis constructions. Additionally, the fixtures needed to allow operators to easily install parts and remove the fully welded assembly with minimal effort, as efficiency and ergonomics are crucial in a production environment.
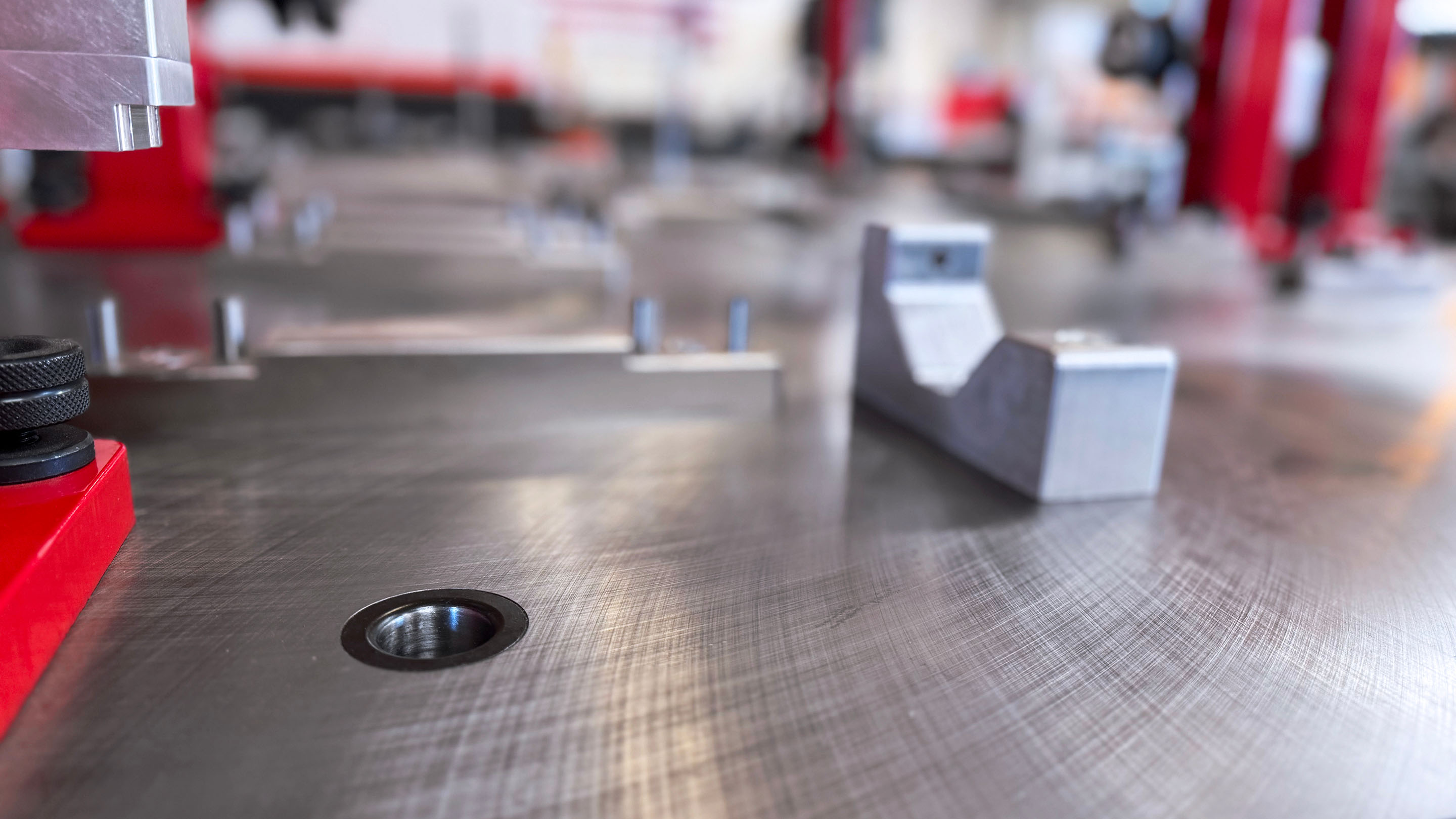
APE developed a series of weld fixtures incorporating laser-cut plates, machined components, and fabricated tube frames. These fixtures transformed what was once an almost insurmountable task into a series of straightforward steps that could be performed by minimally trained technicians.
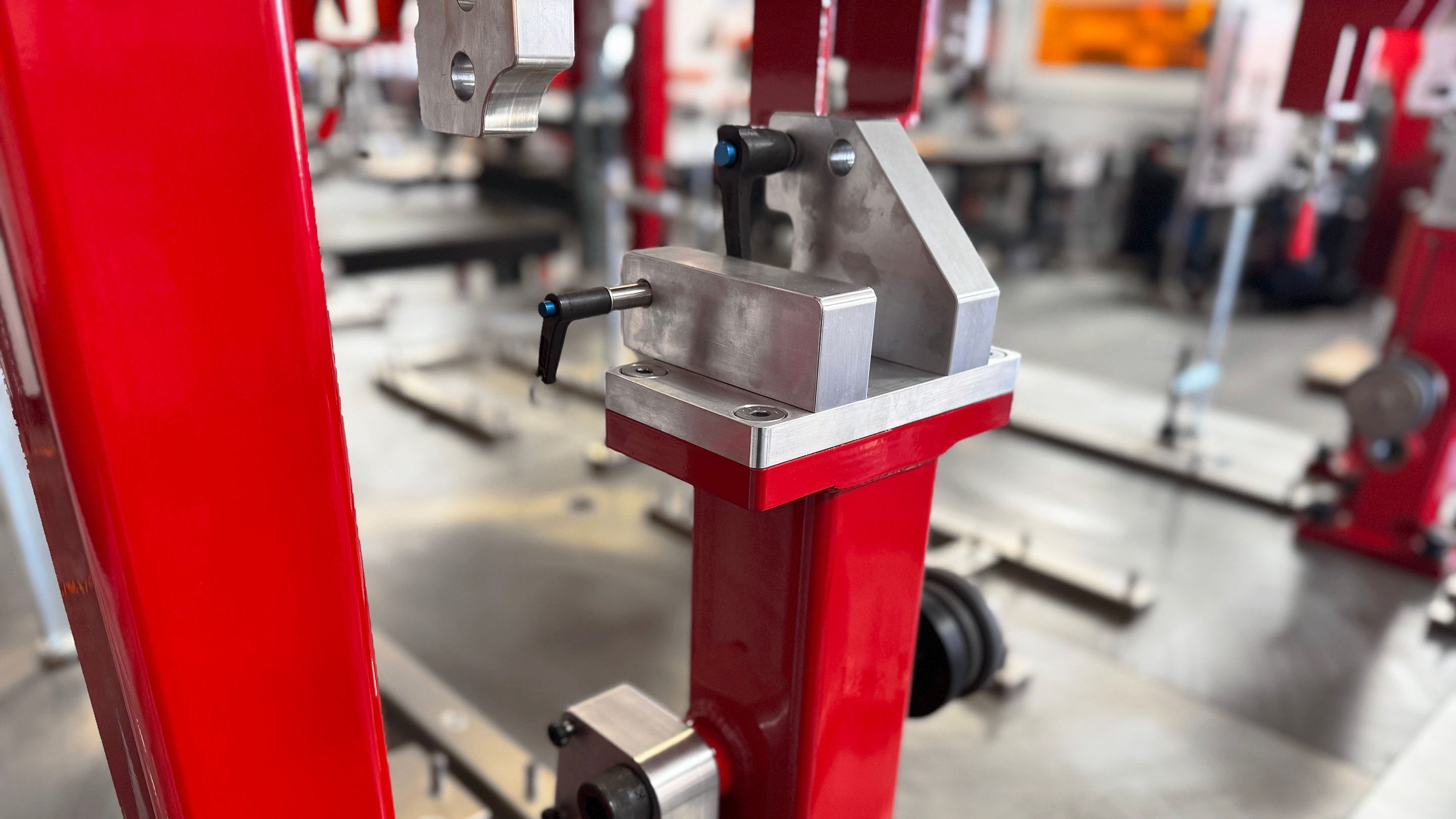
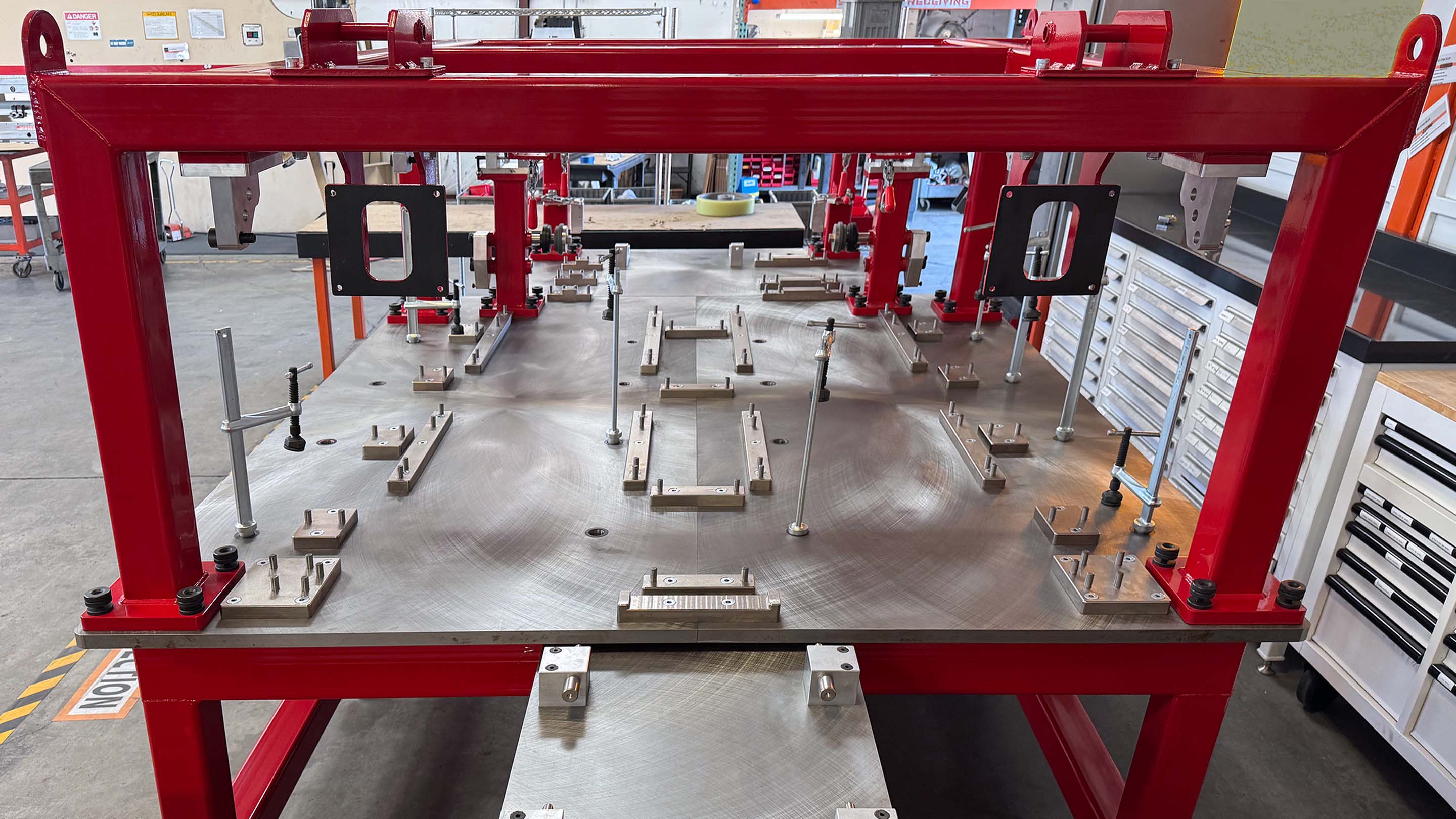
The introduction of these weld fixtures streamlined the assembly process, significantly reducing the complexity and time required to build the chassis. This not only ensured the client could meet their delivery deadlines but also positioned them to expand their business more rapidly in the future.
By partnering with APE, the military vehicle manufacturer gained a reliable and efficient solution to their fixturing and manufacturing challenges, enabling them to focus on further innovation and growth.
APE’s expertise in developing advanced weld fixtures exemplifies how strategic partnerships can enhance a company’s capabilities and accelerate product development. This collaboration underscores APE’s commitment to providing solutions that meet the most demanding industry standards and delivery requirements.
Contact us today to learn how APE can help accelerate your product development process.
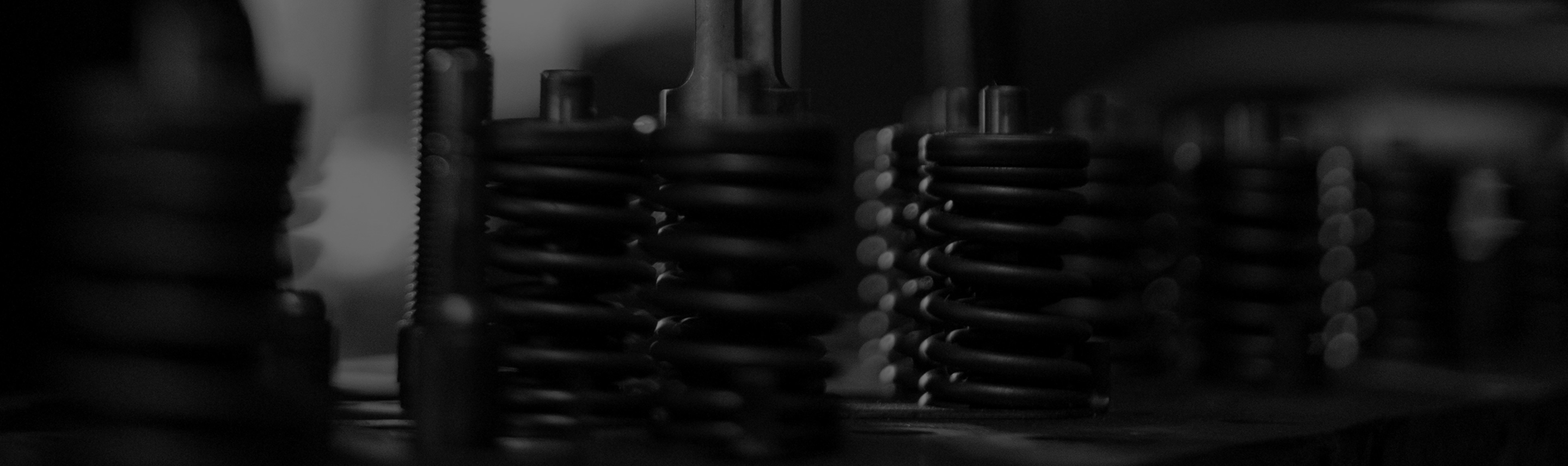
Related Case
Studies
Explore our recent case studies showcasing innovative solutions for advanced manufacturing.
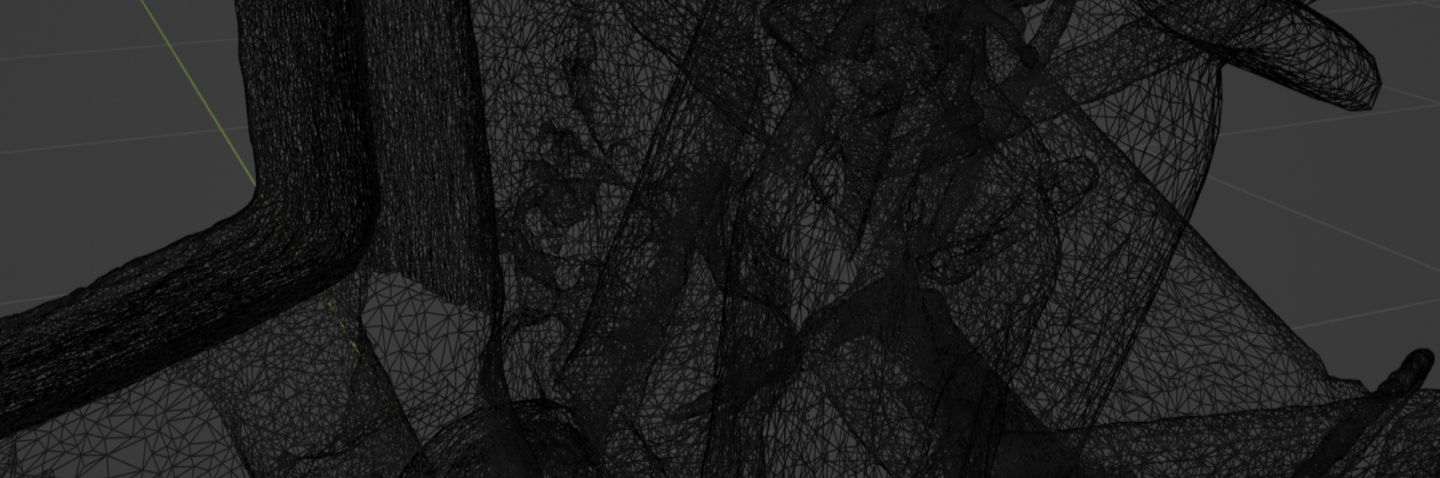
What Else Do We Do? Design And Engneering
Explore our comprehensive design and engineering services that lay the foundation for innovative and effective soluttions. From Concept to planning, every project is meticulously crafted to meet your needds.
Quality & Certifications
At APE, quality is woven into every part of our project life cycle. From design verification to the raw materials we use, to final assembly, our AS9100 certified quality management system... Read more