Portable Jib Crane (PJC)
Creation and Global Deployment of the Portable Jib Crane
The story of our Portable Jib Crane begins with an industrial manufacturing company facing a challenge: they needed to lift a 150-pound component repeatedly throughout their manufacturing process.
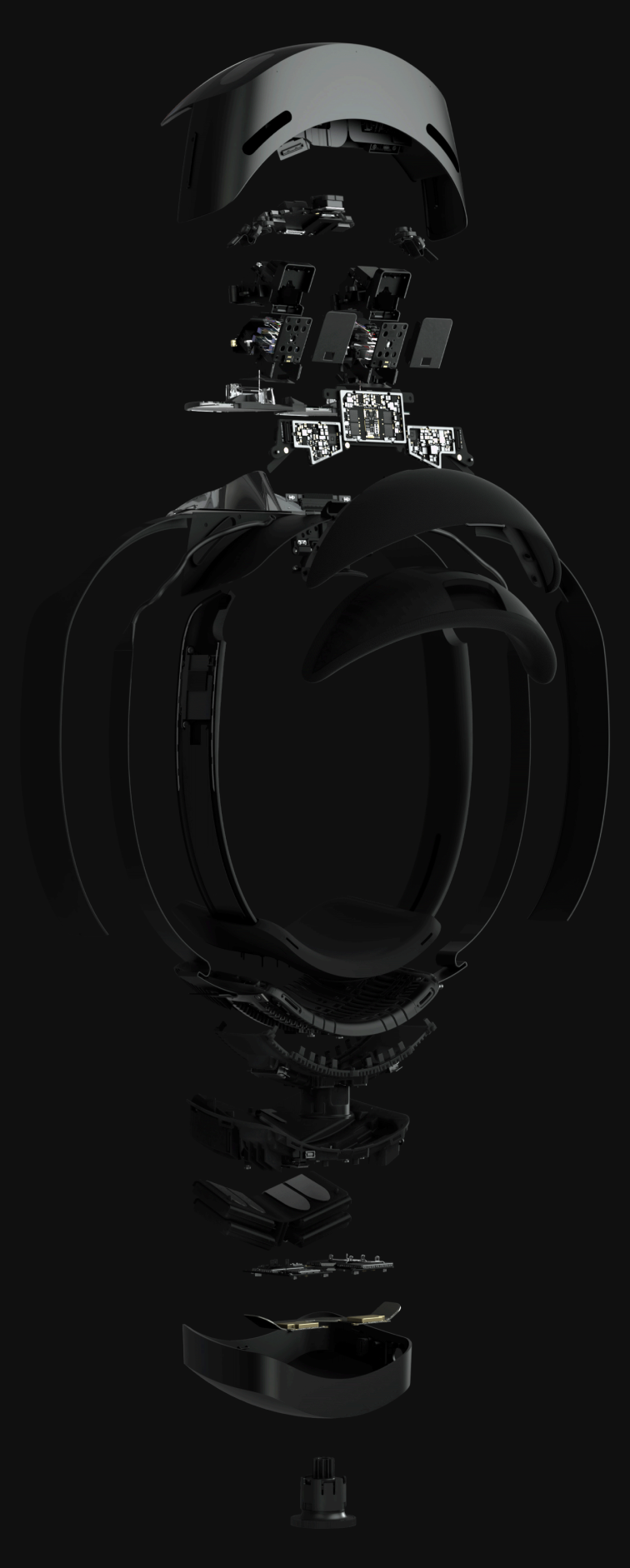
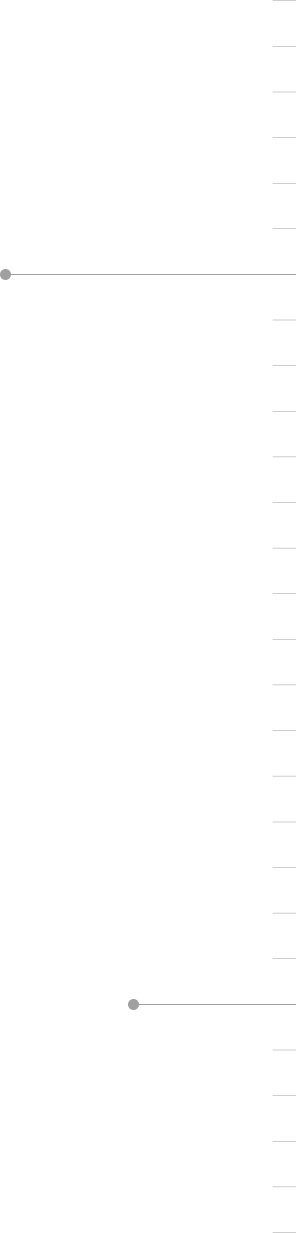
The Finished Product
Portable Jib Crane (PJC)
Creation and Global Deployment of the Portable Jib Crane
The story of our Portable Jib Crane begins with an industrial manufacturing company facing a challenge: they needed to lift a 150-pound component repeatedly throughout their manufacturing process.
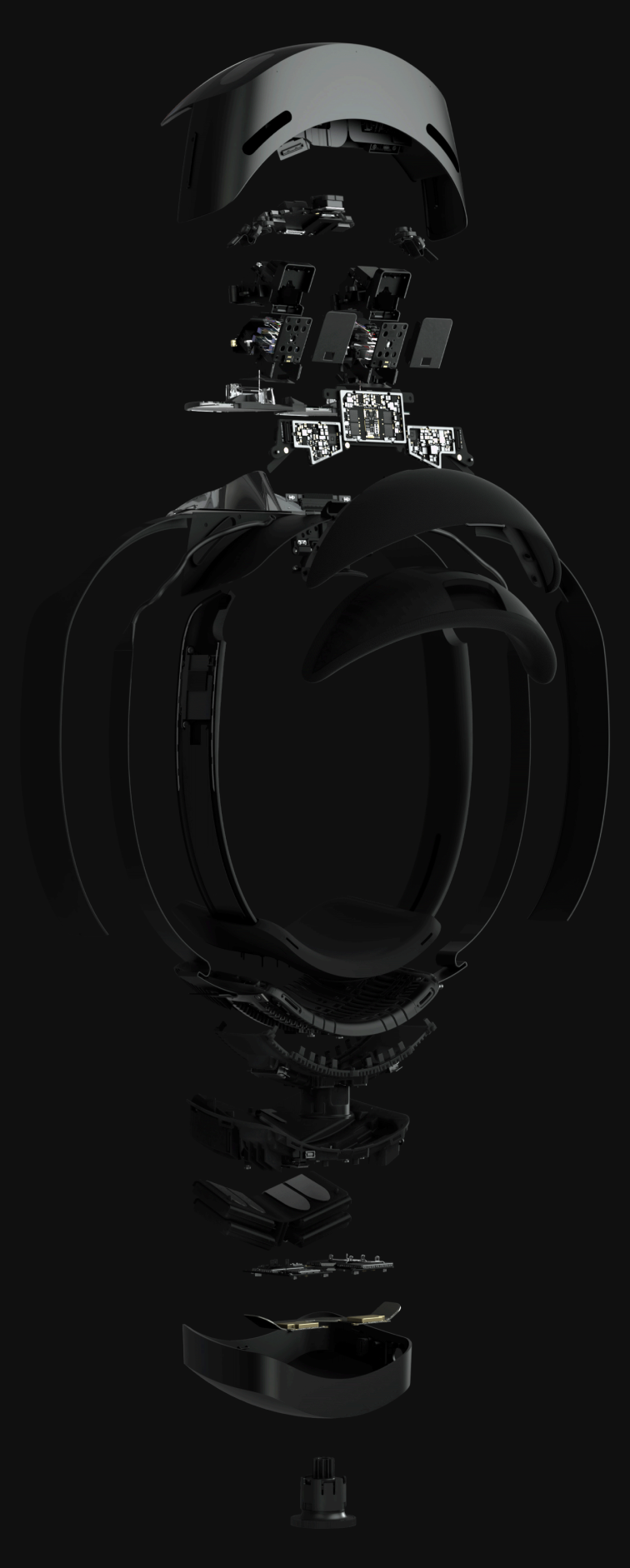
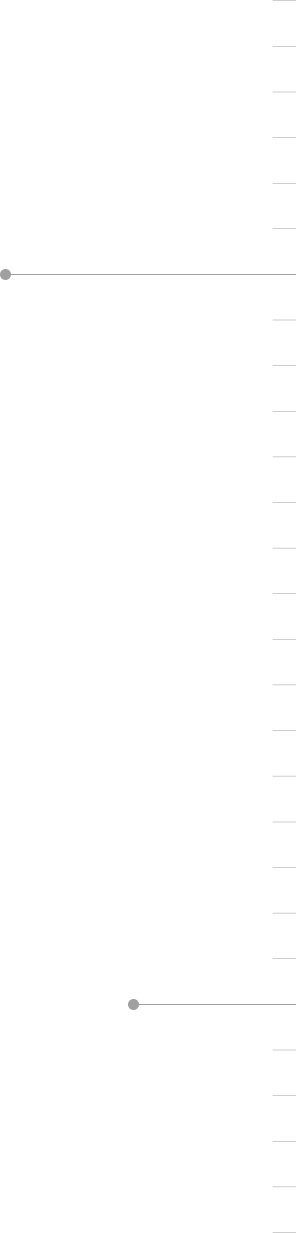
HOW WE MADE IT HAPPEN
In the fast-paced world of new product development, resources and time are often limited. To overcome these challenges, companies can turn to APE for expert assistance to accelerate their development processes. This case study highlights how APE supported a military vehicle manufacturer in meeting critical delivery deadlines by developing an efficient weld fixturing system and manufacturing process.
As the military vehicle manufacturer approached the final stages of designing their latest vehicle, they faced a significant hurdle. They lacked both the in-house expertise and the bandwidth to develop the necessary fixturing system and manufacturing process to meet their delivery requirements. Recognizing the urgency, they reached out to APE for a solution.
APE’s expertise in developing advanced weld fixtures exemplifies how strategic partnerships can enhance a company’s capabilities and accelerate product development. This collaboration underscores APE’s commitment to providing solutions that meet the most demanding industry standards and delivery requirements.
Contact us today to learn how APE can help accelerate your product development process.
The Finished Product
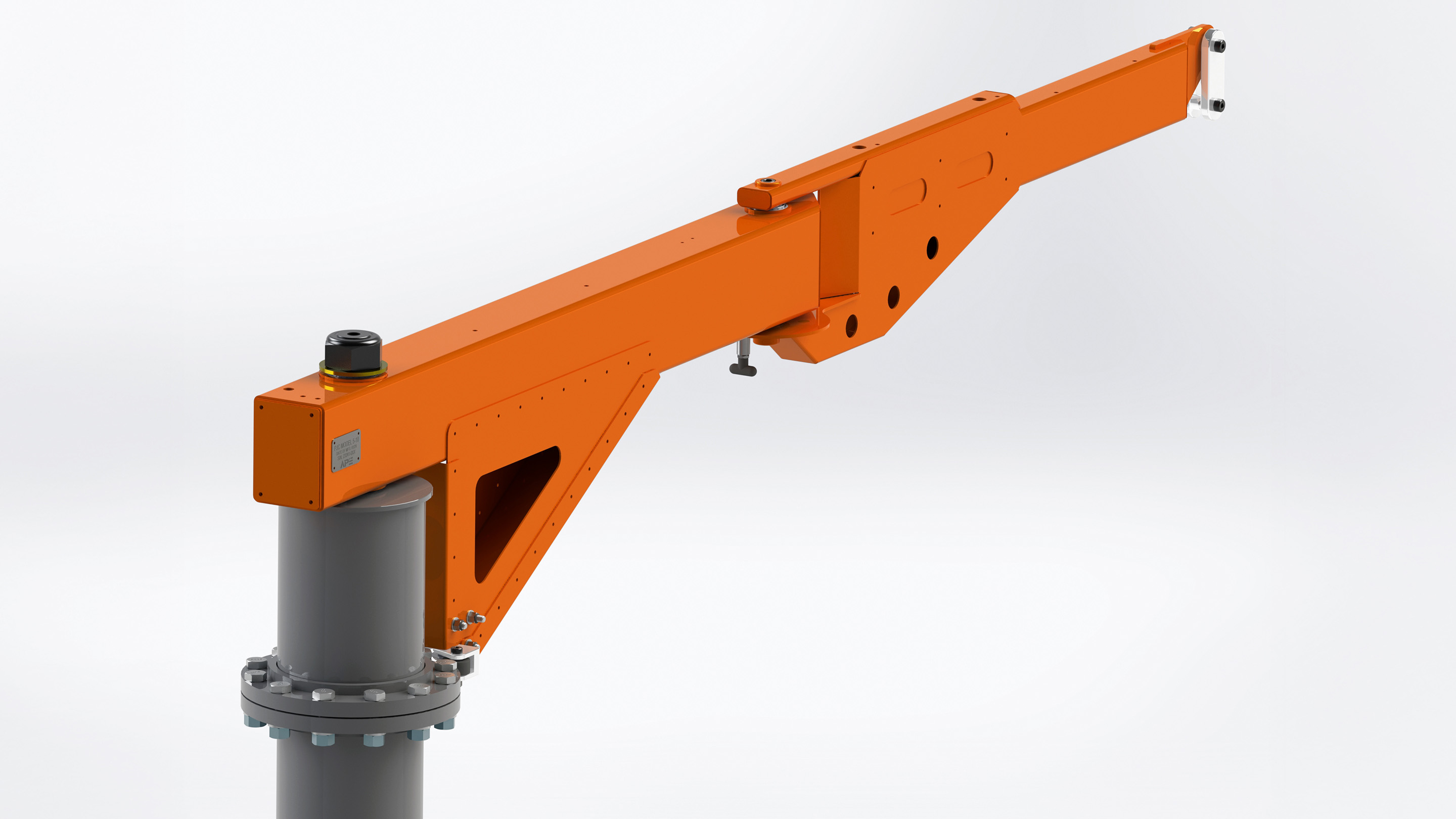
Portable Jib Crane (PJC)
Creation and Global Deployment of the Portable Jib Crane
The story of our Portable Jib Crane begins with an industrial manufacturing company facing a challenge: they needed to lift a 150-pound component repeatedly throughout their manufacturing process.
The Finished Product
HOW WE MADE
IT HAPPEN
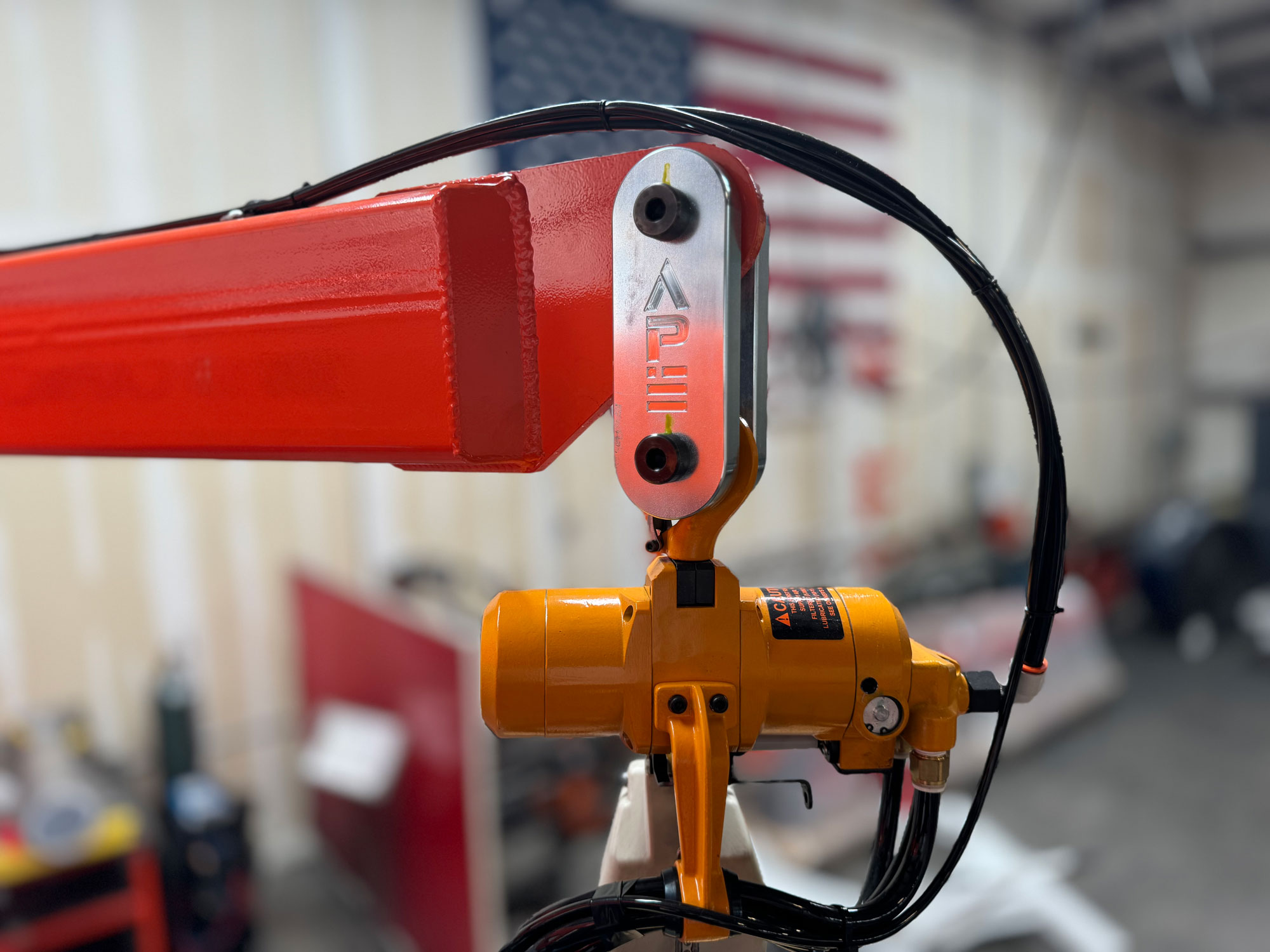
The story of our Portable Jib Crane begins with an industrial manufacturing company facing a challenge: they needed to lift a 150-pound component repeatedly throughout their manufacturing process. This weight was too cumbersome for manual handling yet too small to justify the constant use of a bridge crane.
To create the portable jib crane, we considered several critical factors, including power supply, geometric constraints, code compliance, ergonomics, and ease of use. After thorough analysis of different stakeholder concerns, we began designing the crane using SolidWorks for both component design and finite element analysis. We simulated various load cases and calculated the crane's capacity in accordance with OSHA, ASME, and CMAA standards. Our design was then sent out for third-party verification and received a Professional Engineer’s stamp.
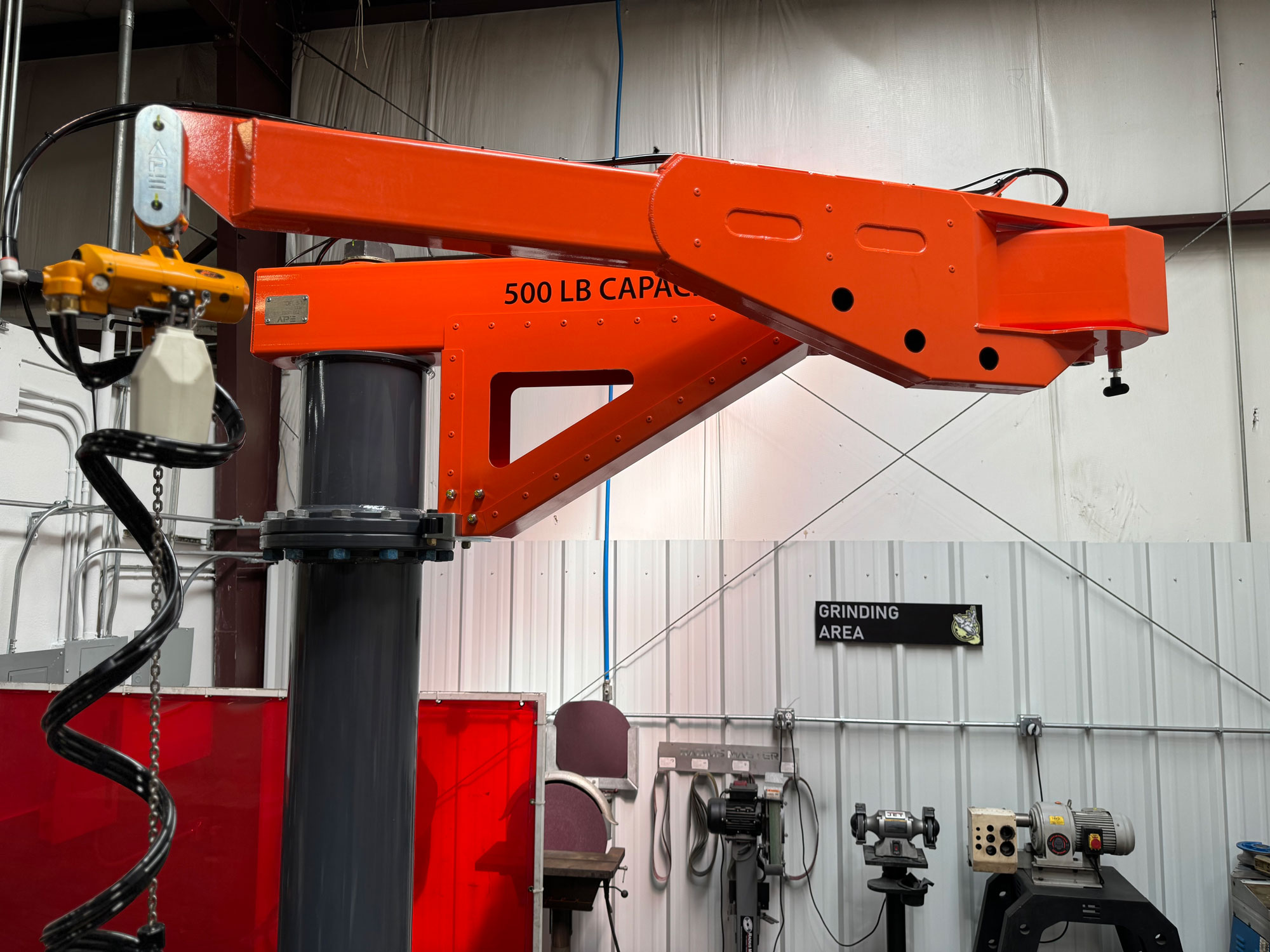
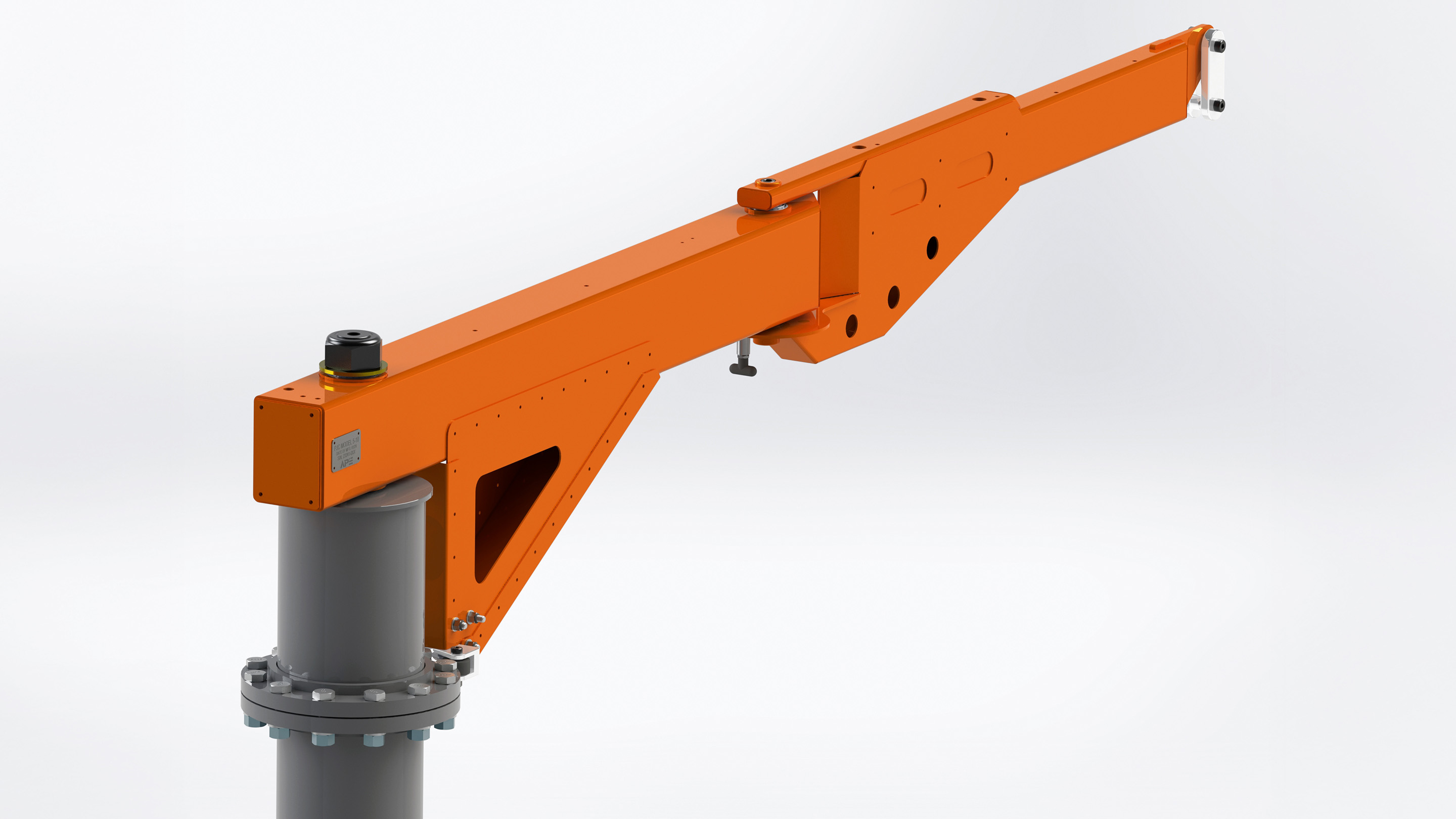
The final design allows for 360-degree rotation of the main boom and 320 degrees of rotation of the secondary boom, making the crane compact, fast, and easy to use within a 20-foot diameter circle. Operating with air-powered hoists and swing brakes, the crane requires only compressed shop air. A built-in hose reel enables quick and easy positioning anywhere in the shop, including outside or in wet conditions.
One unique feature of the portable jib crane is the splice in the main support post, allowing it to be disassembled for shipment inside a standard shipping container. This feature also simplifies the manufacturing process by enabling the main boom assembly to be built on a bench rather than 10 feet in the air.
Fabricating the portable jib crane involved a range of operations, including small part machining, large diameter lathe turning, press brake forming, and critical welding. Careful analysis of the work sequence and manufacturing tolerances was essential to ensure proper functionality after assembly. Our Design-Thru-Fab methodology incorporates features that aid in the fabrication process, such as tab and slot sheet metal features, Cleco alignment holes, and indexing features for forming sheet metal components.
After fabrication, we conducted a series of load tests across the full range of the crane to proof test both structural and tipping capacity.
The success of this initial project led to the realization that the Portable Jib Crane could benefit many other industrial manufacturers. We began producing these cranes for companies around the world. Today, our Portable Jib Crane is used globally, bringing numerous benefits to manufacturing shops:
- Increased productivity
- Reduced safety hazards
- Usability in small rooms or areas with obstacles where standard jibs cannot operate
- Safe and productive operation with minimal training
- Portability with a forklift or pallet jack
- Usability outdoors or in wet environments
Our journey from a single custom solution to a globally deployed product demonstrates our commitment to innovation and customer-centric design. The Portable Jib Crane continues to revolutionize the way components are handled in manufacturing environments worldwide.
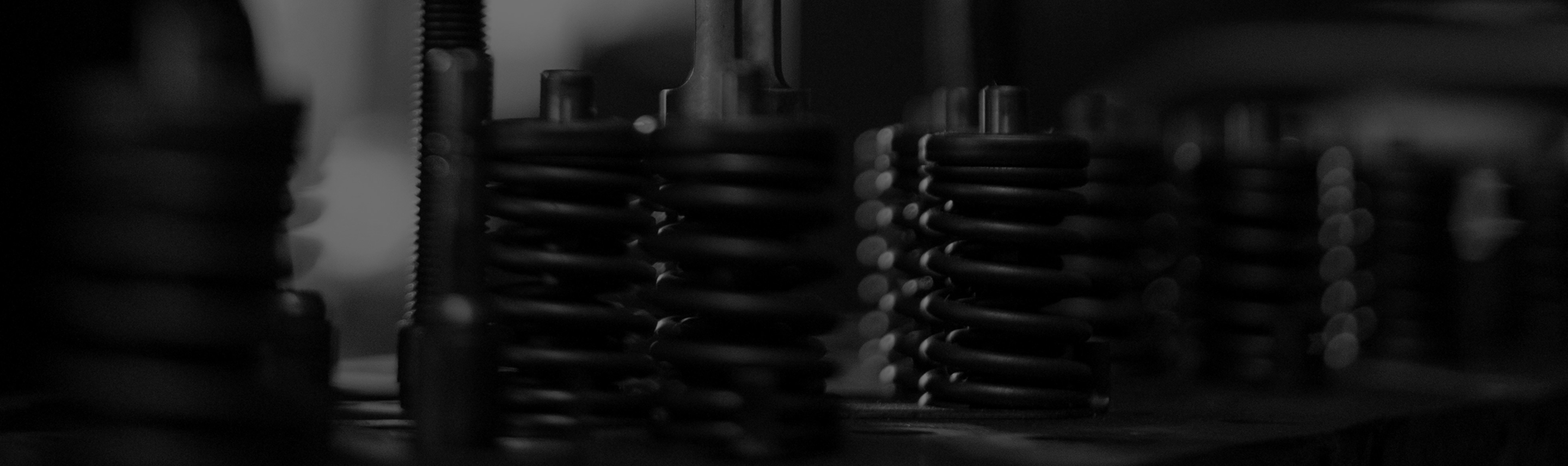
Related Case
Studies
Explore our recent case studies showcasing innovative solutions for advanced manufacturing.
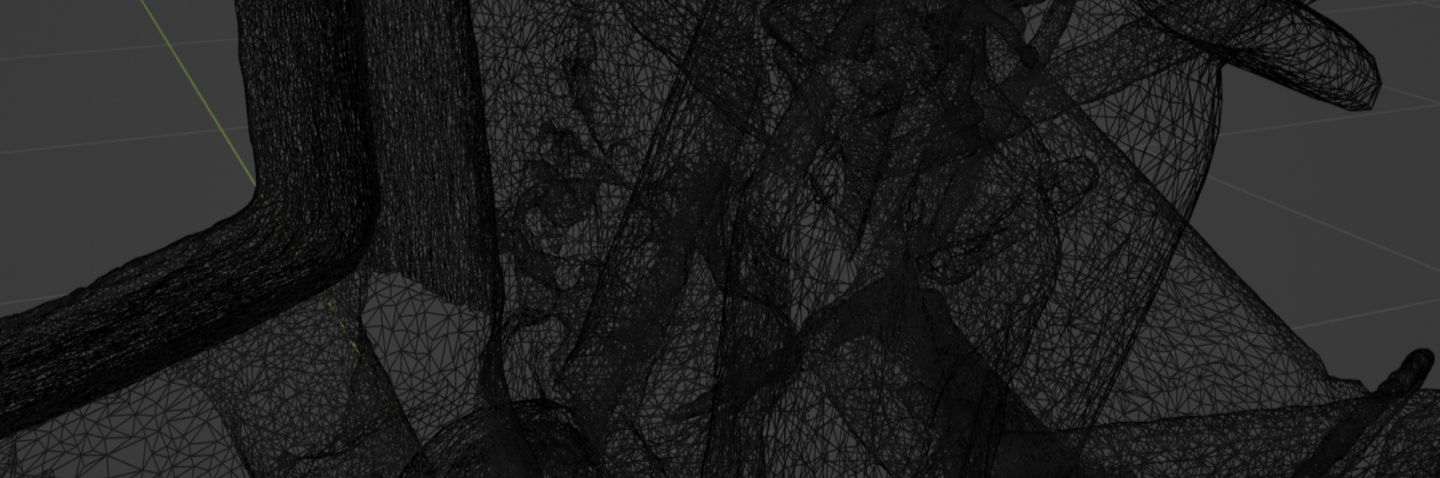
What Else Do We Do? Design And Engneering
Explore our comprehensive design and engineering services that lay the foundation for innovative and effective soluttions. From Concept to planning, every project is meticulously crafted to meet your needds.
Quality & Certifications
At APE, quality is woven into every part of our project life cycle. From design verification to the raw materials we use, to final assembly, our AS9100 certified quality management system... Read more